Benefits of BLS Composite Components
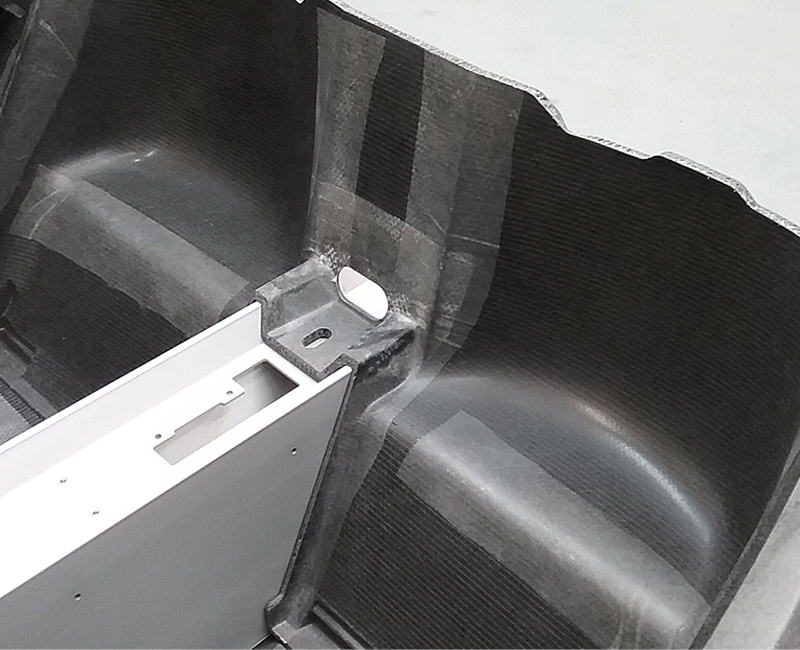
Complex Shapes
Our process can mold complex, deep-drawn designs with variable thicknesses — shapes typically very difficult to create with aluminum or monolithic carbon fiber.
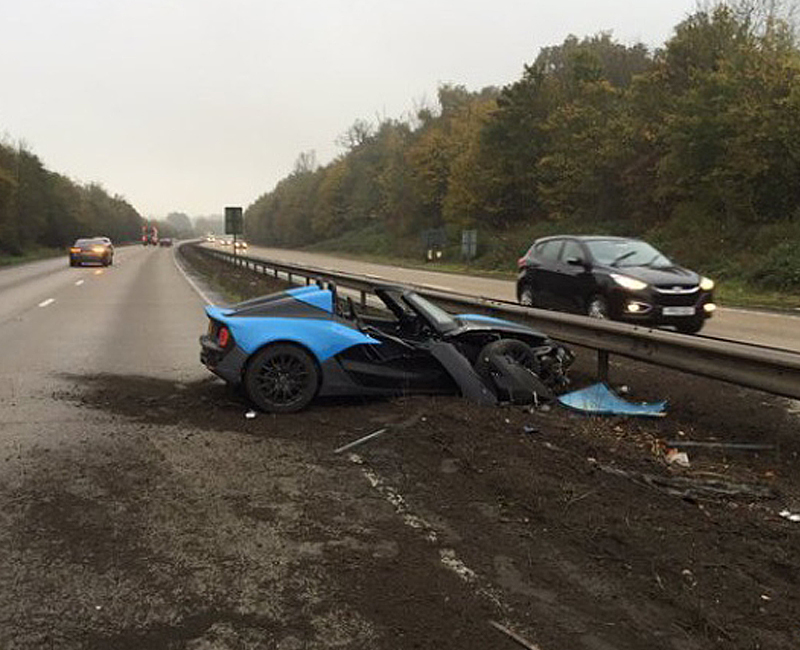
Stiffness & Strength
BLS uses specially formulated, patented resins to maintain the performance properties and strength required for high-speed vehicle crashes.
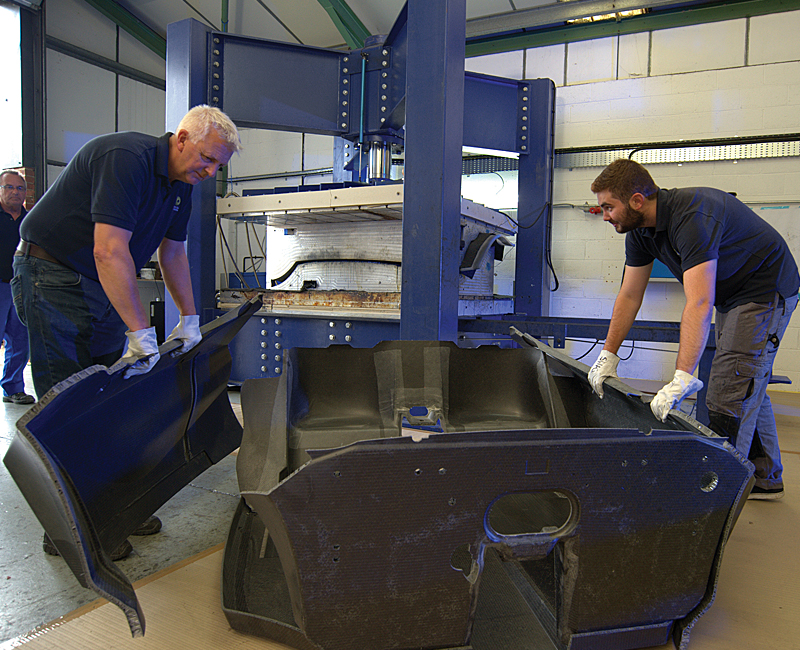
Self-Joining Components
The method used at BLS creates self-joining components. This eliminates the need for jigging or separate fixturing in assembly
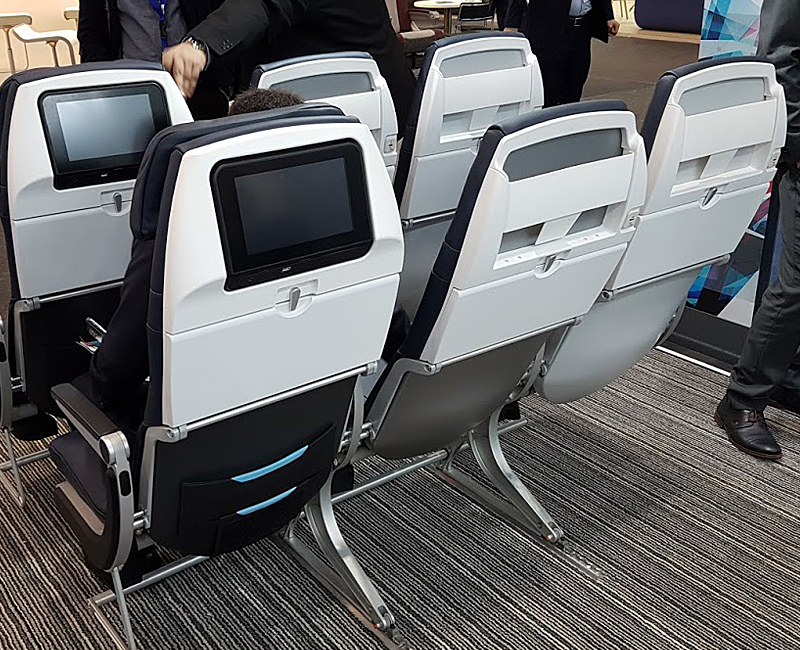
Meets Rigorous Testing
Our composite meets the criteria of FAR 25.853 for FST and OSU Heat Release. It also meets the European Rail Standard EN45545. More >
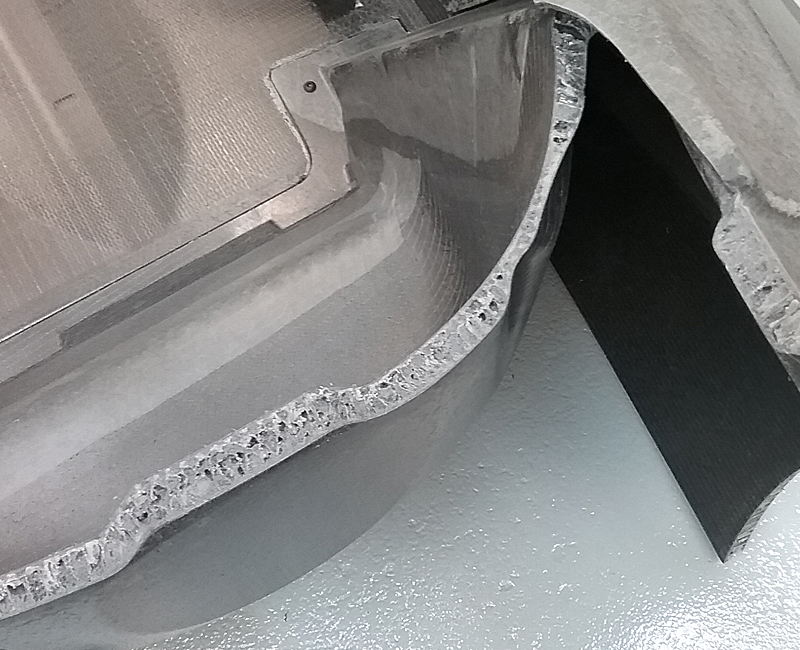
Independent Shapes
Patented sandwich construction allows each side of the material to be shaped independently into different configurations, as needed.
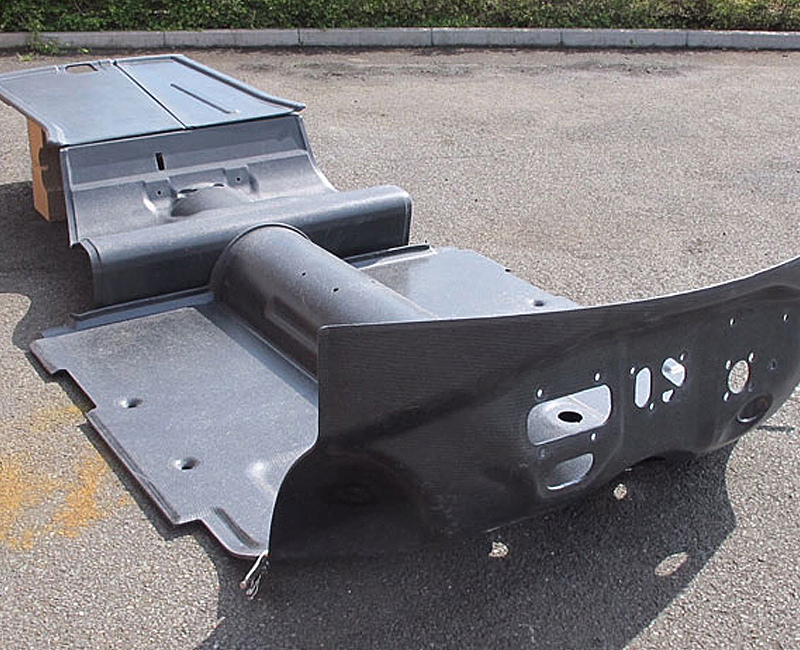
Large Components
Low-pressure BLS presses are able to mold larger components. Compared to multi-part, aluminum chassis , BLS replaces dozens of parts with one part.
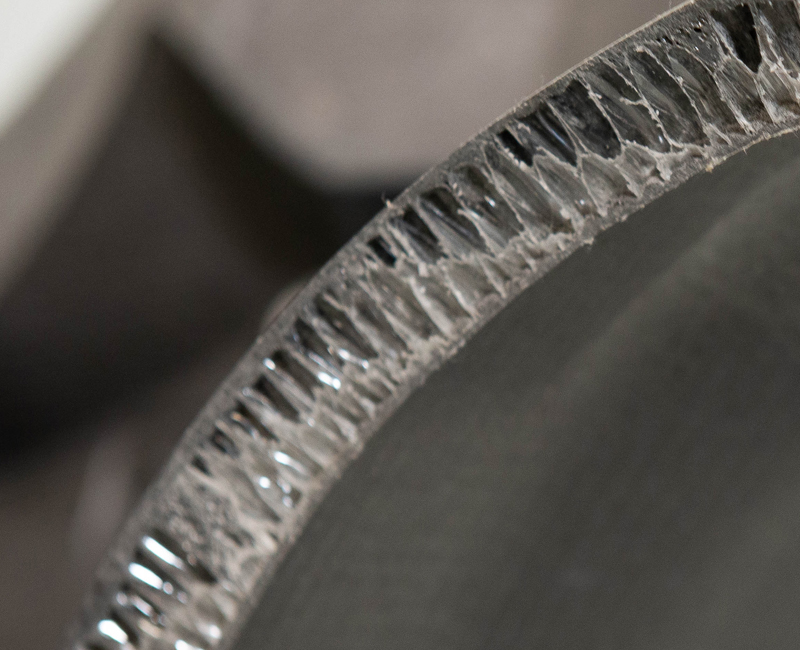
Good Insulation
The sandwich construction used by BLS provides both good heat and sound insulation.
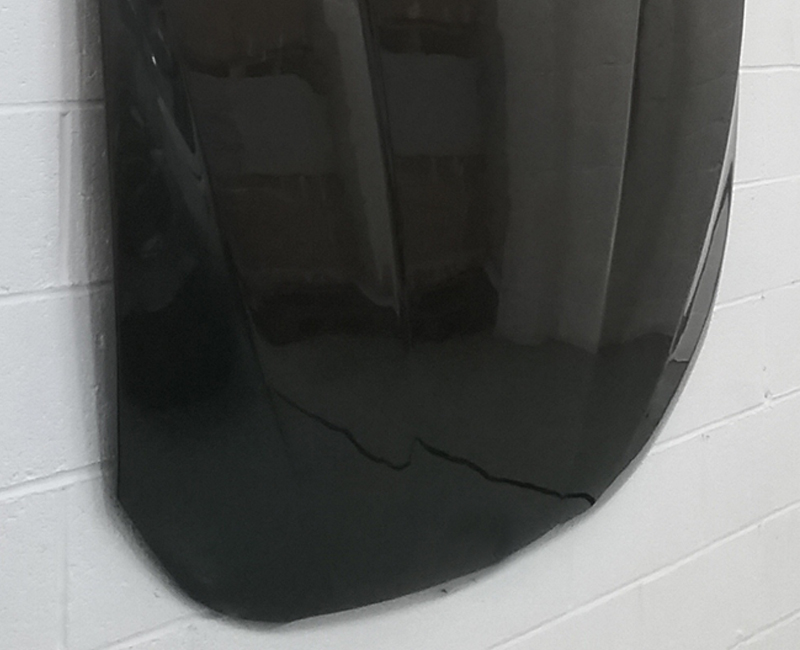
Class A Finishes
The parts made by BLS meet the automotive quality requirements for the finish.