Automotive Chassis & Structural Elements
Objective: Design and manufacture chassis and structural components that are light-weight, stiff and pass all crash test requirements. Be cost competitive and environmentally friendly, and meet high-volume requirements.
BLS Solution
- • Created weight savings
- • Created fuel savings
- • Reduced part count (BOM) and assembly cost
- • Fatigue tested to meet stiffness requirements
- • Molded construction created complex shapes
- • Combined recycled carbon fiber and recycled polycarbonate core
- • Cost competitive with aluminum
- • Helps meet EU CO2 requirements
- • Required less capital investment
- • Provides good sound and heat insulation
- • Manufactured in volumes from 100 to 50,000
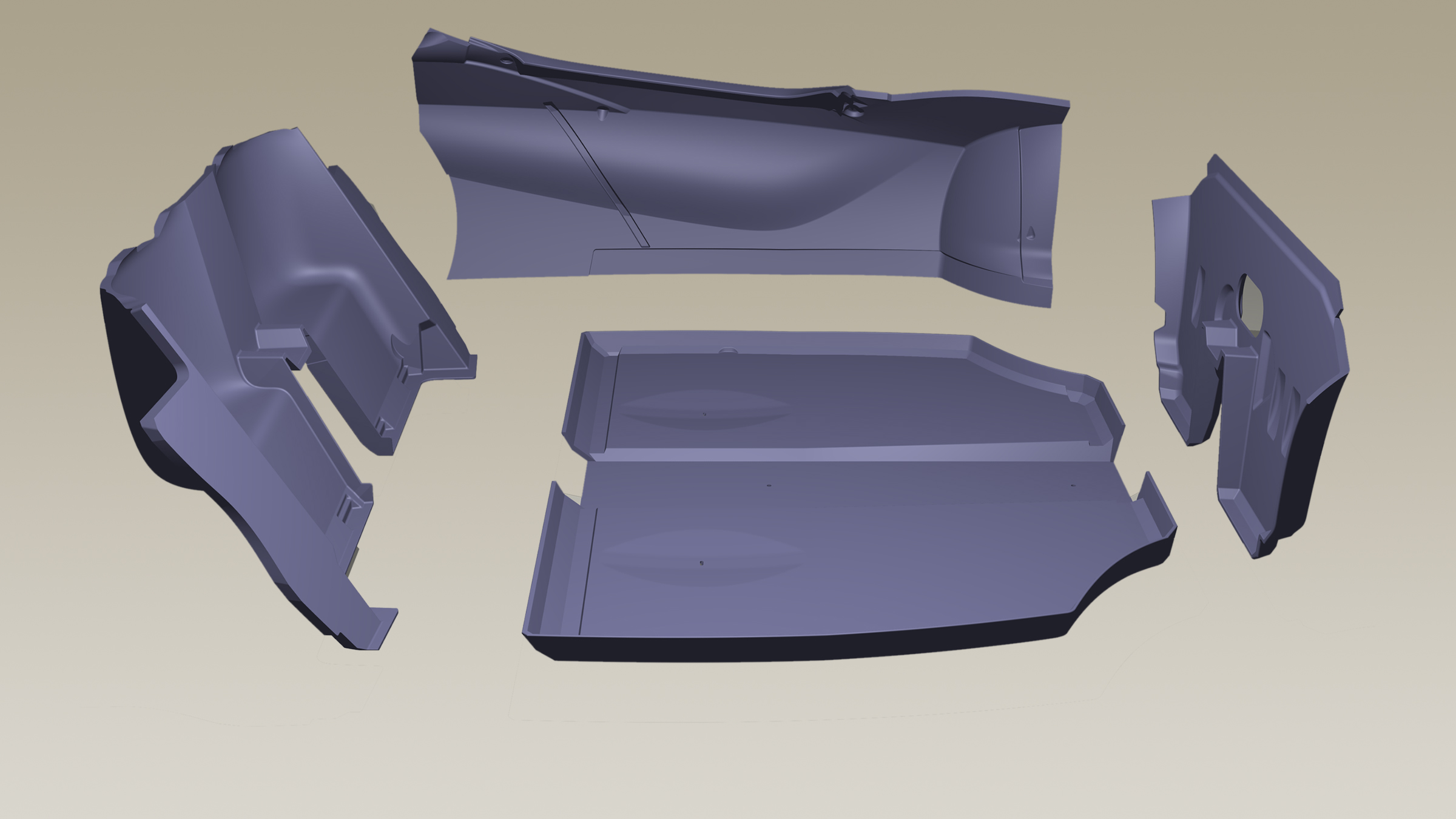
The BLS designed Zenos chassis is made of only five parts. Second side panel not shown in this cut-away.
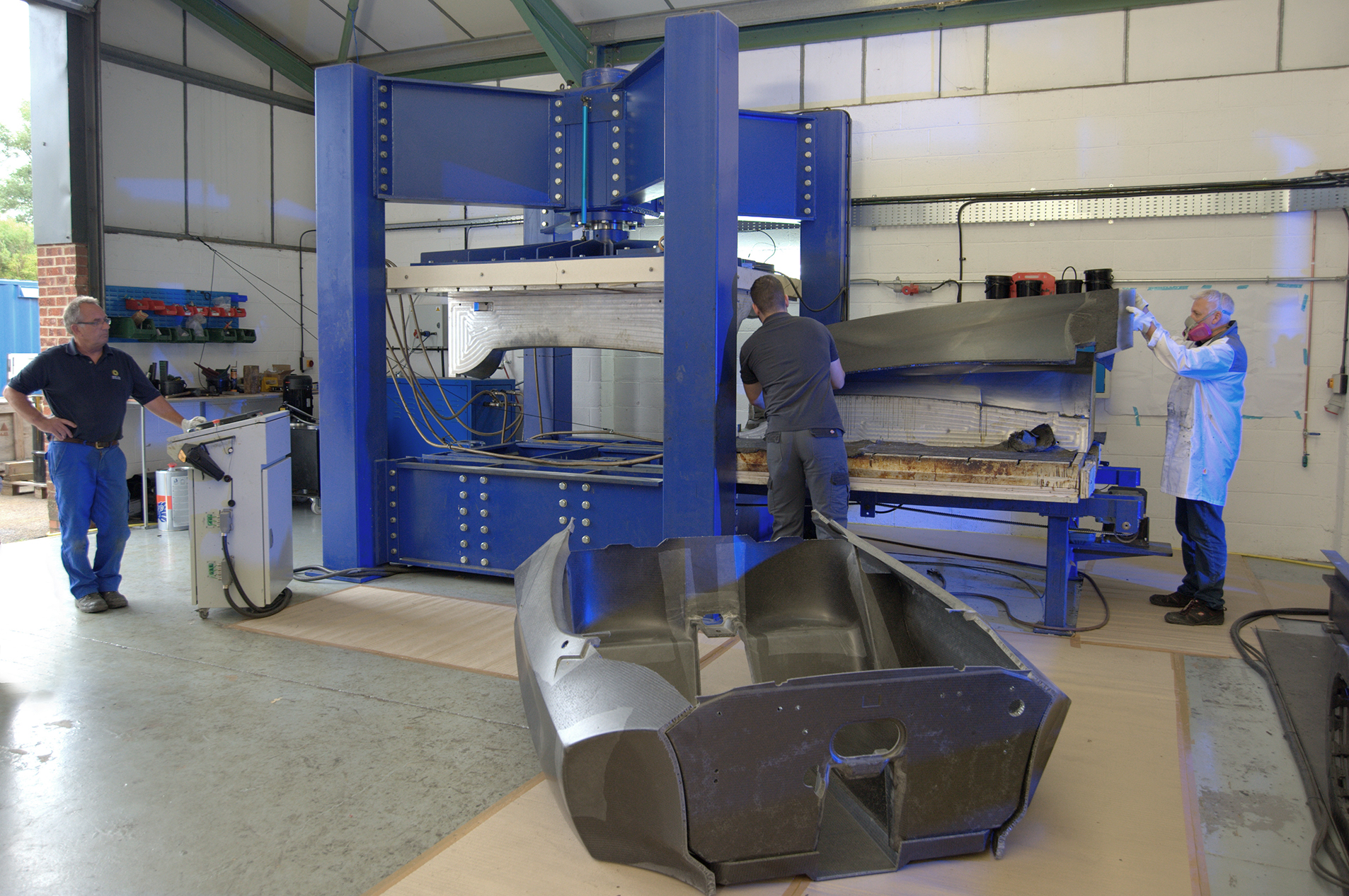
The chassis is self-jigging, substantially reducing assembly time and costs.
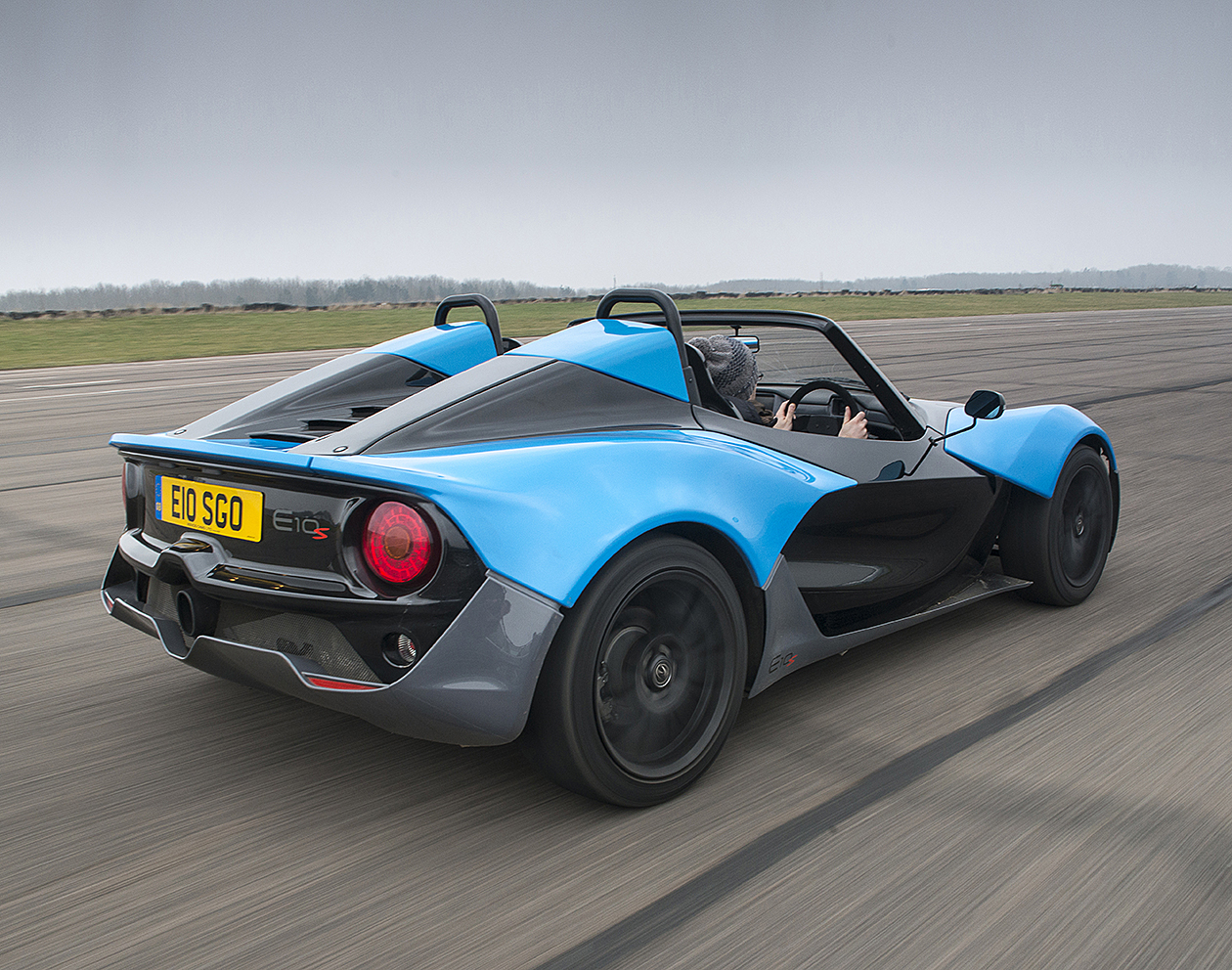
The Zenos E10 with BLS chassis. BLS components can have a Class A finish. This permits components to be used on the exterior, seen here on the door panel.
How did we make a strong, light-weight five-piece chassis for this sports car? Check out this short video and see why our composite technology is better than conventional carbon.